Injection Molding China: Revolutionizing Manufacturing Techniques
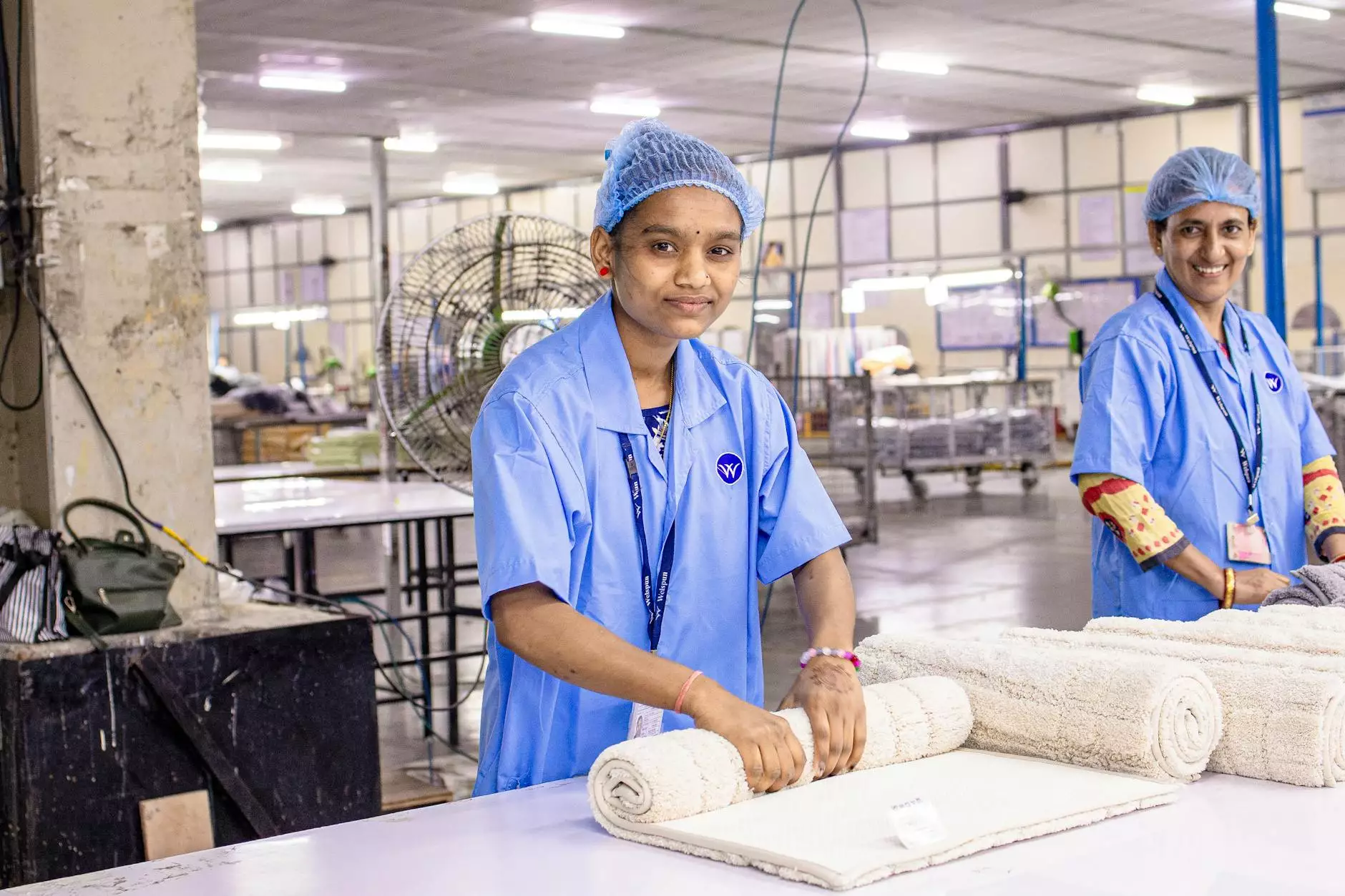
Injection molding has fundamentally transformed the landscape of manufacturing, particularly in China, where companies like Deep Mould are leading the charge. This method allows for the mass production of parts and components with precision and efficiency, fostering the growth of industries ranging from automotive to consumer goods. In this article, we will delve into the intricacies of injection molding in China, examining its advantages, processes, and future trends that are shaping the industry.
1. Understanding Injection Molding
At its core, injection molding is a manufacturing process used to produce parts by injecting molten material into a mold. The materials commonly used include various types of plastics and metals, leading to a variety of applications across different industries. The process is characterized by several distinct steps:
- Material Preparation: The raw materials, often in the form of pellets, are first heated until they melt.
- Injection: The molten material is then injected into a mold under high pressure.
- Cooling: Once the mold is filled, the material cools and solidifies in the desired shape.
- Extraction: Finally, the finished part is ejected from the mold once it has sufficiently hardened.
2. Advantages of Injection Molding in China
China has emerged as a global leader in injection molding for several reasons. Here are some key advantages:
2.1 Cost-Efficiency
The sheer scale of manufacturing in China allows companies to produce parts at a fraction of the cost compared to other countries. With low labor costs and numerous suppliers, businesses can benefit from reduced expenditure without compromising on quality.
2.2 High Production Rates
Injection molding is one of the most efficient manufacturing methods available. It can produce large quantities of identical parts in a short time, making it ideal for businesses looking to scale rapidly. This efficiency is crucial for high-demand industries, including electronics and automotive.
2.3 Precision and Quality
Advanced technology and experienced labor in China ensure that products meet high standards of quality and precision. The use of advanced molds and control systems allows for the production of detailed and complex designs that would be difficult or costly to achieve with other methods.
2.4 Material Versatility
Injection molding can accommodate a wide range of materials, including various polymers, metals, and even composites. This versatility allows businesses to explore innovative solutions tailored to specific requirements.
3. The Injection Molding Process Explained
Understanding the process in detail is critical for businesses considering injection molding for their production needs:
3.1 Designing the Mold
The first step in injection molding involves mold design. This is crucial as the mold determines the final shape and features of the product. Deep Mould employs cutting-edge technologies and software for precision mold design, allowing for complex geometries and functionality.
3.2 Material Selection
Choosing the right material is vital for a successful injection molding process. Engineers at Deep Mould assist clients in selecting materials that meet their functional requirements while also ensuring cost-effectiveness.
3.3 Creating Prototypes
Before mass production, creating prototypes enables testing and refinement. This step ensures that any potential issues can be addressed without incurring costly errors during full production.
3.4 Production and Quality Control
Once the mold is approved, mass production can begin. Rigorous quality control measures are employed throughout the process to ensure each part meets the established specifications. Chinese manufacturers are known for their detailed inspection processes, which safeguard product integrity.
4. Industries Benefiting from Injection Molding in China
The versatility of injection molding means it plays a crucial role across various sectors:
- Automotive: Injection molding is fundamental in producing components such as dashboards, enclosures, and brackets.
- Consumer Electronics: Numerous electronic devices use injection-molded parts to ensure lightweight and durable designs.
- Medical Devices: Precision and biocompatibility make injection molding ideal for manufacturing medical instruments and devices.
- Consumer Goods: Everyday products like kitchenware and toys often rely on injection molding for cost-effective mass production.
5. Challenges Facing the Injection Molding Industry in China
Despite its advantages, the injection molding industry in China does face challenges:
5.1 Environmental Concerns
The production of plastic materials and subsequent waste poses significant environmental challenges. Many manufacturers are now seeking sustainable practices, including recycling materials and using biodegradable polymers.
5.2 Quality Variability
While many factories maintain high standards, variability in quality can be an issue with numerous suppliers. Companies like Deep Mould prioritize consistent quality through stringent checks and control measures.
5.3 Competition and Market Saturation
As the industry grows, competition increases, often leading to price wars. This puts pressure on manufacturers to innovate and improve efficiencies continually.
6. Future Trends in Injection Molding in China
The foresight of injection molding in China points toward several exciting trends:
6.1 Automation and Industry 4.0
The integration of advanced technologies and automation is expected to revolutionize the industry. Industry 4.0 technologies, including IoT and AI, will enhance precision, reduce human error, and improve production efficiency.
6.2 Sustainable Manufacturing Practices
In response to environmental challenges, manufacturers are increasingly adopting eco-friendly practices. This includes using recycled materials and investing in cleaner production methods to minimize the carbon footprint.
6.3 The Rise of Hybrid Manufacturing
Hybrid manufacturing processes, which combine injection molding with additive manufacturing techniques, are gaining popularity. This approach allows for greater flexibility and complexity in design, catering to niche markets with specific needs.
7. Conclusion: Partnering with Leaders in Injection Molding
As we have explored, injection molding in China presents numerous benefits—including cost-efficiency, high production rates, and precision. Companies like Deep Mould are at the forefront of this industry, ready to provide state-of-the-art solutions tailored to specific business needs.
For businesses looking to scale production while maintaining quality, partnering with a manufacturer that understands the nuances of injection molding is critical. By leveraging advanced technologies, robust supply chains, and experienced personnel, companies can ensure they stay ahead in an increasingly competitive market.
To learn more about how Deep Mould can support your business in navigating the injection molding landscape in China, visit deepmould.net today!
injection molding china